The first step in developing a Parachute Recovery System (PRS) for a commercial drone is the flight termination system (FTS). The FTS is the mechanism which stops the propellers from spinning. It is activated when a drone failure is detected by the pilot manually deploying through the Manual Triggering Device (MTD) or through the Automatic Triggering System (ATS).
The FTS is critical for the overall parachute safety system for two main reasons:
- You do not want the propellers to tangle with the parachute lines, as this prevents the parachute from properly opening.
- You need the propellers to stop spinning to prevent lacerations in a situation where the aircraft falls on a person. As I’m sure many who are reading this would know, the propellers can be sharp, and the purpose of the product is for the safety of people.
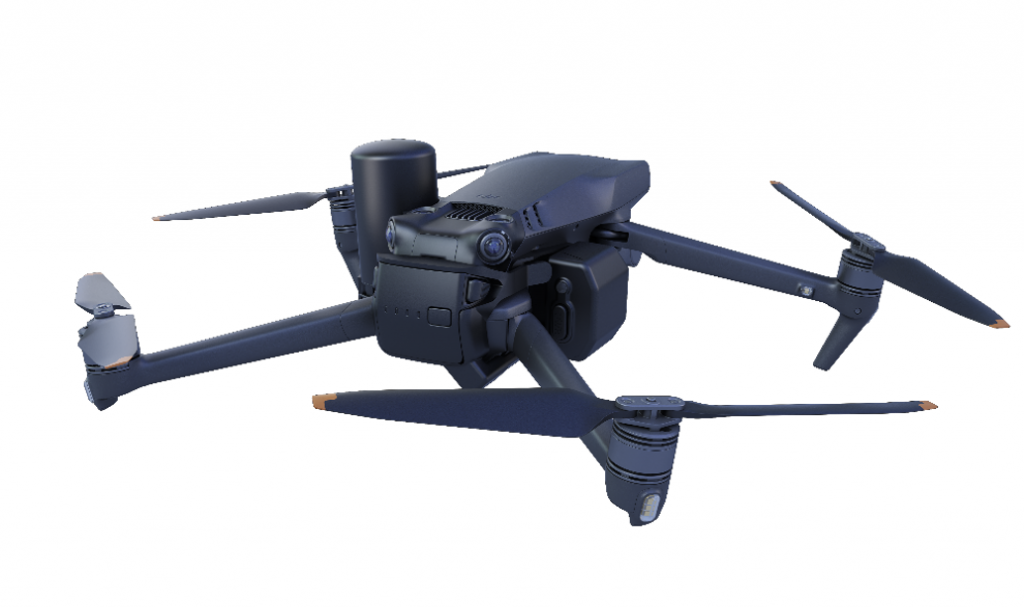
Developing the Flight Termination System (FTS)
One of the more challenging aspects of the development of the parachute recovery system for retrofit products is the development of the FTS.
There are two ways to stop the propellers from spinning. The first solution to look for when building an FTS is a software interface — for example, the DJI Matrice 300 RTK’s On-Board Software Development Kit (OSDK). In this instance, the software is used to send a “Kill Command” to stop the signal to the drone’s control board. This will stop the motors from spinning.
The second method is to use a physical, “electrical” FTS. This method involves developing a mechanical and electrical add-on that goes between the battery and the drone. This method is used when an OSDK-like option is not available and does add additional weight to the overall PRS. AVSS builds the FTS first in order to understand the effects of the additional weight, how it affects the ATS failure tuning, and the maximum takeoff weight of the drone.
When it comes to the DJI Mavic 3, it was clear from the day it was announced that there was not an OSDK or other software solution for the FTS. Because of this, AVSS developed an electrical FTS that fits between the battery and the drone itself. When designing the FTS for the Mavic 3, AVSS focused on an attachment that would still enable the removal and easy swapping of the battery. It was also designed to ensure the system could be removed when the pilot does not require the PRS.
Bracket Development
The next step when it comes to the development of any parachute recovery system is how it will attach to the drone itself. AVSS has standard parts that have passed rigorous certification testing in the past and prefers to use these parts across all of their systems.
When it comes to bracket development, there are a few things to consider. First of all, the design of the bracket is done in such a way that you don’t need tools when installing the bracket on site. AVSS has numerous customers in public safety. The last thing customers want to deal with is bolts and tools during a critical life-saving mission.
The next thing to consider when developing a bracket system is utilizing the existing DJI case. After talking to many customers, AVSS has learned that parachute systems are often unused because the bracket system doesn’t fit in the existing case or can’t be easily removed after flight. When this happens, the parachute is often disregarded as it becomes inconvenient for the pilot.
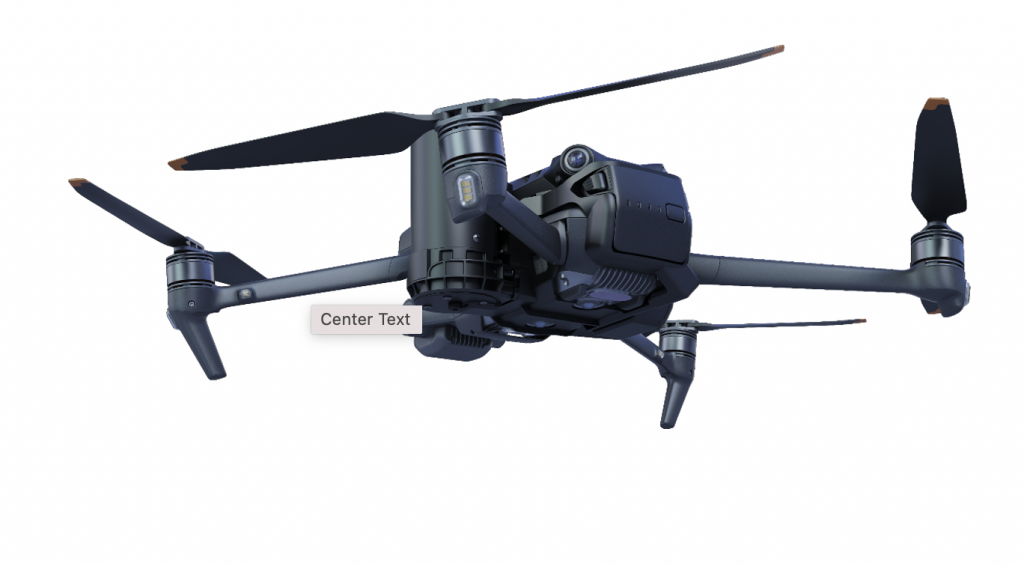
Testing the Bracket
Additionally, from a technical perspective, the bracket is designed to withstand the opening shock of the parachute deployment. During ASTM F3322 testing, five tests are completed where the drone must freefall for three seconds. It must approach terminal velocity, and then the parachute is deployed. This aggressive testing is used to demonstrate that the PRS has been built with a sufficient safety factor.
AVSS carefully chooses the materials needed to ensure a lightweight solution is designed, while also ensuring that the forces can be taken. This often means using carbon fibre for larger drone solutions.
In summary, when selecting a parachute recovery system for flight over people, pilots should ask the following questions:
- How will the propellers stop spinning before deployment?
- How easy is it for the pilot to use and remove the PRS?